Fabricante de molde para injeção: soluções sob medida para produção
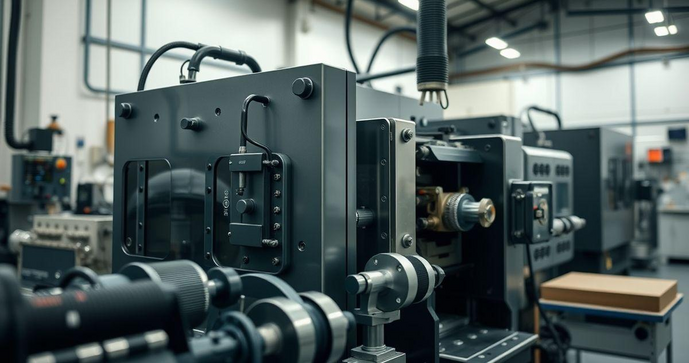
Por: Leonardo - 30 de Abril de 2025
O setor industrial tem se beneficiado enormemente da tecnologia de moldagem por injeção, que permite a produção em massa de peças com alta precisão e eficiência. A escolha do fabricante de molde para injeção é um fator crucial para garantir a qualidade e a durabilidade dos produtos finais. Neste artigo, abordaremos as principais características que um bom fabricante deve ter, as vantagens de optar por fornecedores locais, como avaliar a qualidade dos moldes e as tendências atuais do mercado. Entender esses aspectos pode ajudar empresas a otimizar sua produção e alcançar melhores resultados.
Principais características de um bom fabricante de molde para injeção
Escolher um fabricante de molde para injeção é uma decisão crítica que pode impactar diretamente a qualidade e a eficiência da produção. Um bom fabricante deve apresentar uma série de características que garantam não apenas a entrega de produtos de alta qualidade, mas também um serviço confiável e suporte contínuo. A seguir, discutiremos as principais características que um fabricante deve ter para se destacar no mercado.
1. Experiência e Expertise
A experiência é um dos fatores mais importantes a serem considerados ao escolher um fabricante de molde para injeção. Um fabricante com anos de atuação no mercado possui um conhecimento profundo sobre os processos de moldagem, os materiais utilizados e as melhores práticas para garantir a qualidade do produto final. Além disso, a expertise em diferentes tipos de moldes, como moldes de injeção de plástico, metal e outros materiais, é fundamental para atender a uma variedade de necessidades dos clientes.
2. Tecnologia Avançada
Um bom fabricante deve estar atualizado com as últimas tecnologias e inovações no setor de moldagem por injeção. Isso inclui o uso de software de design assistido por computador (CAD) e simulação de moldes, que permitem a criação de projetos mais precisos e eficientes. Além disso, a utilização de máquinas modernas e automatizadas pode aumentar a precisão e a velocidade da produção, resultando em moldes de maior qualidade e menor tempo de entrega.
3. Capacidade de Personalização
Cada projeto de moldagem por injeção é único e pode exigir soluções personalizadas. Um fabricante de qualidade deve ser capaz de oferecer serviços de personalização, adaptando os moldes às especificações exatas do cliente. Isso inclui a capacidade de trabalhar com diferentes materiais, tamanhos e complexidades de design. A flexibilidade para atender às necessidades específicas do cliente é um diferencial importante que pode influenciar a escolha do fabricante.
4. Controle de Qualidade Rigoroso
Um bom fabricante deve ter um sistema de controle de qualidade rigoroso em todas as etapas do processo de produção. Isso inclui a verificação de materiais, a inspeção de moldes durante a fabricação e testes finais para garantir que os moldes atendam aos padrões de qualidade exigidos. A implementação de normas de qualidade, como ISO 9001, é um indicativo de que o fabricante se compromete a manter altos padrões de qualidade e a satisfação do cliente.
5. Suporte e Atendimento ao Cliente
O suporte ao cliente é uma característica essencial de um bom fabricante de molde para injeção. Isso inclui a disponibilidade para responder a perguntas, fornecer orientações sobre o uso e manutenção dos moldes e oferecer assistência técnica quando necessário. Um fabricante que valoriza o relacionamento com o cliente e está disposto a oferecer suporte contínuo pode ajudar a resolver problemas rapidamente e garantir a continuidade da produção.
6. Transparência e Comunicação
A transparência nas operações e a comunicação clara são fundamentais para um relacionamento saudável entre o fabricante e o cliente. Um bom fabricante deve ser capaz de fornecer informações detalhadas sobre o processo de produção, prazos de entrega e custos. Além disso, a comunicação aberta sobre quaisquer desafios ou mudanças no projeto é crucial para evitar mal-entendidos e garantir que as expectativas sejam atendidas.
7. Portfólio de Projetos Anteriores
Um fabricante de qualidade deve ter um portfólio de projetos anteriores que demonstre sua capacidade e experiência. Analisar trabalhos anteriores pode fornecer insights sobre a qualidade dos moldes produzidos, a variedade de projetos atendidos e a satisfação dos clientes. Um portfólio diversificado é um bom indicativo de que o fabricante possui a experiência necessária para lidar com diferentes tipos de moldes e setores.
8. Compromisso com a Sustentabilidade
Nos dias de hoje, a sustentabilidade é uma preocupação crescente em todos os setores, incluindo a fabricação de moldes para injeção. Um bom fabricante deve estar comprometido com práticas sustentáveis, como a utilização de materiais recicláveis e a implementação de processos que minimizem o desperdício. Isso não apenas contribui para a preservação do meio ambiente, mas também pode ser um diferencial competitivo no mercado.
Em resumo, ao escolher um fabricante de molde para injeção, é fundamental considerar características como experiência, tecnologia, personalização, controle de qualidade, suporte ao cliente, transparência, portfólio e compromisso com a sustentabilidade. Um fabricante que reúne essas qualidades estará mais bem preparado para atender às suas necessidades e garantir a qualidade dos produtos finais. Para mais informações sobre soluções de moldes, você pode conferir a Ferramentaria de moldes plasticos.
Vantagens de escolher um fabricante local de molde para injeção
Optar por um fabricante local de molde para injeção pode trazer uma série de benefícios significativos para empresas que buscam eficiência, qualidade e um bom relacionamento comercial. A escolha de um fornecedor próximo não apenas facilita a logística, mas também pode impactar positivamente a produção e a satisfação do cliente. A seguir, discutiremos as principais vantagens de escolher um fabricante local para suas necessidades de moldagem por injeção.
1. Redução de Custos de Transporte
Um dos principais benefícios de trabalhar com um fabricante local é a redução dos custos de transporte. Quando os moldes são produzidos em uma localização próxima, os gastos com frete e logística são significativamente menores. Isso não apenas diminui os custos operacionais, mas também pode acelerar o tempo de entrega, permitindo que as empresas respondam mais rapidamente às demandas do mercado. A economia em transporte pode ser um fator decisivo, especialmente para pequenas e médias empresas que buscam otimizar seus orçamentos.
2. Comunicação Eficiente
Trabalhar com um fabricante local facilita a comunicação. A proximidade geográfica permite reuniões presenciais, o que pode ser crucial para discutir detalhes do projeto, realizar ajustes e resolver problemas rapidamente. A comunicação face a face tende a ser mais eficaz do que a comunicação remota, pois permite uma troca de informações mais clara e direta. Além disso, a possibilidade de visitas regulares à fábrica pode proporcionar uma melhor compreensão dos processos de produção e das capacidades do fabricante.
3. Flexibilidade e Agilidade
Fabricantes locais geralmente têm mais flexibilidade para atender às necessidades específicas de seus clientes. Eles podem adaptar rapidamente os processos de produção e realizar alterações nos moldes conforme necessário. Essa agilidade é especialmente importante em um ambiente de negócios dinâmico, onde as demandas podem mudar rapidamente. A capacidade de fazer ajustes em tempo real pode resultar em uma produção mais eficiente e em produtos que atendem melhor às expectativas do cliente.
4. Suporte Técnico e Assistência Rápida
Um fabricante local pode oferecer suporte técnico mais acessível e rápido. Em caso de problemas com os moldes ou a produção, a assistência pode ser fornecida de forma imediata, minimizando o tempo de inatividade. Isso é particularmente importante em indústrias onde a continuidade da produção é essencial. Ter um contato próximo com o fabricante permite que as empresas resolvam problemas rapidamente, garantindo que a produção não seja interrompida por longos períodos.
5. Conhecimento do Mercado Local
Fabricantes locais geralmente têm um conhecimento mais profundo do mercado em que atuam. Eles entendem as necessidades e preferências dos clientes da região, o que pode resultar em produtos mais adequados e competitivos. Esse conhecimento pode ser um diferencial importante, pois permite que o fabricante desenvolva soluções que atendam melhor às especificidades do mercado local, aumentando a satisfação do cliente e a competitividade dos produtos.
6. Relacionamento Pessoal
Estabelecer um relacionamento pessoal com um fabricante local pode ser extremamente benéfico. A confiança e a colaboração que se desenvolvem ao longo do tempo podem levar a parcerias mais fortes e produtivas. Um bom relacionamento pode facilitar a negociação de preços, prazos e condições de pagamento, além de promover um ambiente de trabalho mais colaborativo. Essa conexão pessoal pode ser um fator motivador para ambas as partes, resultando em um compromisso mútuo com a qualidade e a satisfação do cliente.
7. Contribuição para a Economia Local
Escolher um fabricante local também significa apoiar a economia da região. Ao optar por fornecedores locais, as empresas ajudam a criar e manter empregos na comunidade, contribuindo para o desenvolvimento econômico local. Isso pode ter um impacto positivo na qualidade de vida da população e na sustentabilidade da economia regional. Além disso, muitos consumidores valorizam empresas que demonstram responsabilidade social e compromisso com a comunidade.
8. Sustentabilidade e Redução da Pegada de Carbono
Trabalhar com fabricantes locais pode contribuir para práticas mais sustentáveis. A redução da distância de transporte não apenas diminui os custos, mas também reduz a pegada de carbono associada ao transporte de mercadorias. Além disso, muitos fabricantes locais estão adotando práticas sustentáveis em seus processos de produção, utilizando materiais recicláveis e implementando tecnologias que minimizam o desperdício. Isso pode ser um diferencial importante para empresas que buscam se posicionar como ambientalmente responsáveis.
Em resumo, escolher um fabricante local de molde para injeção oferece uma série de vantagens, incluindo redução de custos, comunicação eficiente, flexibilidade, suporte técnico rápido, conhecimento do mercado, relacionamentos pessoais, contribuição para a economia local e práticas sustentáveis. Para empresas que buscam otimizar sua produção e garantir a qualidade dos produtos, trabalhar com empresas de injeção plástica locais pode ser uma estratégia inteligente e eficaz.
Como avaliar a qualidade dos moldes para injeção
A avaliação da qualidade dos moldes para injeção é um passo crucial para garantir que os produtos finais atendam aos padrões de qualidade e eficiência desejados. Moldes de alta qualidade não apenas melhoram a precisão e a consistência da produção, mas também reduzem custos e tempo de inatividade. A seguir, apresentamos algumas diretrizes e critérios que podem ser utilizados para avaliar a qualidade dos moldes para injeção.
1. Materiais Utilizados
Um dos primeiros aspectos a considerar na avaliação da qualidade de um molde é o tipo de material utilizado em sua fabricação. Moldes de injeção são frequentemente feitos de aço ou alumínio, e a escolha do material pode impactar diretamente a durabilidade e a resistência do molde. O aço, por exemplo, é mais durável e resistente ao desgaste, tornando-se ideal para produções em larga escala. Já o alumínio é mais leve e pode ser mais econômico, mas pode não suportar o mesmo nível de desgaste que o aço. Portanto, é importante verificar se o fabricante utiliza materiais de alta qualidade e adequados para o tipo de produção desejada.
2. Processos de Fabricação
A qualidade dos moldes também depende dos processos de fabricação utilizados. Um bom fabricante deve empregar técnicas avançadas de usinagem e fabricação, como a ferramentaria e usinagem, que garantem precisão e qualidade na produção dos moldes. A utilização de tecnologia de ponta, como máquinas CNC (Controle Numérico Computadorizado), pode aumentar a precisão e a repetibilidade dos moldes, resultando em produtos finais de alta qualidade. Além disso, a implementação de processos de controle de qualidade durante a fabricação é essencial para identificar e corrigir problemas antes que os moldes sejam entregues ao cliente.
3. Design do Molde
O design do molde é outro fator crítico que deve ser avaliado. Um bom molde deve ser projetado para facilitar a injeção do material, minimizar a formação de bolhas de ar e garantir um fluxo uniforme do material. Além disso, o design deve considerar a facilidade de manutenção e reparo, permitindo que ajustes sejam feitos rapidamente, caso necessário. Moldes bem projetados também devem incluir características como sistemas de resfriamento eficientes, que ajudam a controlar a temperatura durante o processo de injeção e garantem a qualidade do produto final.
4. Tolerâncias e Dimensões
A precisão das tolerâncias e dimensões do molde é fundamental para a qualidade do produto final. Moldes de alta qualidade devem ser capazes de manter tolerâncias rigorosas, garantindo que as peças injetadas tenham as dimensões corretas e se encaixem perfeitamente. A verificação das tolerâncias deve ser realizada durante o processo de fabricação e também após a conclusão do molde. Isso pode incluir medições com instrumentos de precisão, como micrômetros e paquímetros, para garantir que todas as especificações sejam atendidas.
5. Testes de Funcionalidade
Antes de um molde ser colocado em produção, é essencial realizar testes de funcionalidade. Isso envolve a injeção de material no molde para verificar se ele produz peças de acordo com as especificações desejadas. Durante esses testes, é importante observar a qualidade das peças injetadas, verificando se há defeitos, como rebarbas, bolhas de ar ou deformações. Os testes devem ser documentados e analisados para garantir que o molde atenda aos padrões de qualidade exigidos.
6. Durabilidade e Vida Útil
A durabilidade do molde é um aspecto importante a ser considerado na avaliação da qualidade. Moldes de alta qualidade devem ser projetados para suportar um número significativo de ciclos de injeção sem apresentar desgaste excessivo. A vida útil do molde pode ser influenciada pela escolha dos materiais, pelo design e pelos processos de fabricação. É recomendável que o fabricante forneça informações sobre a expectativa de vida útil do molde e as condições de operação ideais para maximizar sua durabilidade.
7. Suporte e Garantia
Um bom fabricante deve oferecer suporte e garantia para os moldes produzidos. Isso inclui assistência técnica em caso de problemas e a possibilidade de realizar ajustes ou reparos, se necessário. A garantia é um indicativo da confiança do fabricante na qualidade de seus produtos e pode proporcionar tranquilidade ao cliente. É importante verificar as condições da garantia e o nível de suporte oferecido antes de finalizar a compra do molde.
8. Feedback de Clientes Anteriores
Por fim, uma das melhores maneiras de avaliar a qualidade de um fabricante de moldes para injeção é buscar feedback de clientes anteriores. Testemunhos e avaliações podem fornecer insights valiosos sobre a experiência de outros clientes com o fabricante, incluindo a qualidade dos moldes, o atendimento ao cliente e a eficiência do suporte técnico. Pesquisar sobre a reputação do fabricante no mercado pode ajudar a tomar uma decisão mais informada.
Em resumo, a avaliação da qualidade dos moldes para injeção envolve a análise de diversos fatores, incluindo os materiais utilizados, os processos de fabricação, o design do molde, as tolerâncias, os testes de funcionalidade, a durabilidade, o suporte oferecido e o feedback de clientes anteriores. Ao considerar esses aspectos, as empresas podem garantir que estão investindo em moldes de alta qualidade que atenderão às suas necessidades de produção e contribuirão para o sucesso de seus produtos.
Tendências e inovações no mercado de moldes para injeção
O mercado de moldes para injeção tem passado por transformações significativas nos últimos anos, impulsionadas por inovações tecnológicas e mudanças nas demandas do setor industrial. À medida que as empresas buscam aumentar a eficiência, reduzir custos e melhorar a qualidade dos produtos, novas tendências têm surgido, moldando o futuro da fabricação de moldes. Neste artigo, exploraremos algumas das principais tendências e inovações que estão impactando o mercado de moldes para injeção.
1. Impressão 3D na Fabricação de Moldes
A impressão 3D tem se tornado uma ferramenta valiosa na fabricação de moldes para injeção. Essa tecnologia permite a criação rápida de protótipos e moldes, reduzindo significativamente o tempo de desenvolvimento. Com a impressão 3D, os fabricantes podem testar e ajustar designs antes de investir em moldes tradicionais, economizando tempo e recursos. Além disso, a impressão 3D possibilita a produção de geometrias complexas que seriam difíceis ou impossíveis de serem alcançadas com métodos convencionais. Essa inovação está revolucionando a forma como os moldes são projetados e fabricados, permitindo uma maior flexibilidade e personalização.
2. Materiais Avançados
O desenvolvimento de novos materiais tem sido uma tendência crescente no mercado de moldes para injeção. Materiais como plásticos de engenharia, compósitos e ligas metálicas avançadas estão sendo utilizados para criar moldes mais leves, duráveis e resistentes ao desgaste. Esses materiais não apenas melhoram a eficiência da produção, mas também aumentam a vida útil dos moldes, reduzindo a necessidade de manutenção e substituição. A utilização de materiais avançados também permite a fabricação de peças com propriedades específicas, como resistência a altas temperaturas ou resistência química, atendendo a uma variedade de aplicações industriais.
3. Automação e Indústria 4.0
A automação e a Indústria 4.0 estão transformando a maneira como os moldes para injeção são fabricados e gerenciados. A integração de tecnologias como Internet das Coisas (IoT), inteligência artificial e análise de dados está permitindo que os fabricantes monitorem e otimizem seus processos de produção em tempo real. Isso resulta em uma maior eficiência, redução de desperdícios e melhor controle de qualidade. A automação também facilita a personalização em massa, permitindo que os fabricantes atendam a demandas específicas dos clientes de forma mais ágil e eficiente.
4. Sustentabilidade e Práticas Ecológicas
A sustentabilidade tem se tornado uma prioridade para muitas empresas, e o mercado de moldes para injeção não é exceção. Os fabricantes estão adotando práticas ecológicas, como a utilização de materiais recicláveis e a implementação de processos que minimizam o desperdício. Além disso, a eficiência energética nas operações de fabricação está sendo priorizada, com o objetivo de reduzir a pegada de carbono. A crescente demanda por produtos sustentáveis está impulsionando a inovação no design de moldes, levando à criação de soluções que atendem tanto às necessidades dos clientes quanto às exigências ambientais.
5. Digitalização e Simulação
A digitalização tem desempenhado um papel fundamental na modernização do mercado de moldes para injeção. O uso de software de simulação permite que os fabricantes testem e otimizem designs de moldes antes da produção física. Isso não apenas economiza tempo e recursos, mas também ajuda a identificar problemas potenciais que podem surgir durante o processo de injeção. A simulação também permite a análise de fluxo de material, temperatura e pressão, garantindo que os moldes sejam projetados para maximizar a eficiência e a qualidade do produto final.
6. Integração de Tecnologias de Controle de Qualidade
A qualidade é uma preocupação constante na fabricação de moldes para injeção, e a integração de tecnologias de controle de qualidade está se tornando uma tendência importante. Sistemas de monitoramento em tempo real, que utilizam sensores e câmeras, permitem que os fabricantes detectem falhas e inconsistências durante o processo de produção. Isso resulta em uma maior precisão e confiabilidade na fabricação de moldes, garantindo que os produtos finais atendam aos padrões de qualidade exigidos. A implementação de tecnologias de controle de qualidade também pode reduzir o tempo de inatividade e os custos associados a retrabalhos e desperdícios.
7. Personalização e Customização
A personalização tem se tornado uma demanda crescente no mercado de moldes para injeção. Os clientes estão buscando soluções que atendam às suas necessidades específicas, e os fabricantes estão respondendo a essa demanda com a oferta de moldes personalizados. Isso inclui a capacidade de adaptar designs, tamanhos e funcionalidades de acordo com as exigências do cliente. A personalização não apenas melhora a satisfação do cliente, mas também pode resultar em uma vantagem competitiva para os fabricantes que conseguem oferecer soluções sob medida.
8. Colaboração e Parcerias Estratégicas
A colaboração entre fabricantes, fornecedores e clientes está se tornando uma tendência importante no mercado de moldes para injeção. Parcerias estratégicas podem levar a inovações conjuntas, compartilhamento de conhecimentos e desenvolvimento de soluções mais eficazes. A colaboração também pode facilitar a troca de informações sobre tendências de mercado e novas tecnologias, permitindo que as empresas se mantenham atualizadas e competitivas. Essa abordagem colaborativa pode resultar em produtos de maior qualidade e em um processo de desenvolvimento mais ágil.
Em resumo, o mercado de moldes para injeção está em constante evolução, impulsionado por inovações tecnológicas e mudanças nas demandas do setor. Tendências como impressão 3D, materiais avançados, automação, sustentabilidade, digitalização, controle de qualidade, personalização e colaboração estão moldando o futuro da fabricação de moldes. Para empresas que buscam se manter competitivas, é essencial acompanhar essas tendências e adotar inovações que possam melhorar a eficiência e a qualidade dos produtos. A injeção de plastico é um campo em crescimento, e estar atento às novas tecnologias e práticas pode fazer toda a diferença no sucesso da produção.
Em conclusão, a moldagem por injeção é uma tecnologia essencial para o setor industrial, proporcionando eficiência e precisão na produção de peças. A escolha de um fabricante de molde adequado é fundamental para garantir a qualidade e a durabilidade dos produtos finais. Ao considerar as características de um bom fabricante, as vantagens de fornecedores locais, a avaliação da qualidade dos moldes e as tendências do mercado, as empresas podem tomar decisões informadas que impactam positivamente sua produção. Compreender esses aspectos não apenas otimiza processos, mas também contribui para a competitividade e o sucesso a longo prazo no mercado. Investir em moldes de qualidade e acompanhar as inovações do setor são passos cruciais para alcançar resultados satisfatórios e atender às demandas crescentes dos consumidores.